云母带绕包机工作原理图解,从结构解析到工艺优化
发布时间:2025-04-16 浏览:210次
“在电线电缆制造领域,云母带绕包工艺是构建耐火层的关键技术。一台高效稳定的云母带绕包机,直接影响着电力设备在高温环境下的安全性能。”——这段来自某电缆工程师的感慨,揭示了云母带绕包机在工业制造中的核心地位。本文将深入解析这一设备的工作原理图,通过结构拆解与动态流程分析,展现其如何实现精密绕包工艺。
一、云母带绕包机的核心结构设计
云母带绕包机由四大功能模块构成:放卷系统、绕包装置、张力控制系统及收卷系统。每个模块的协同运作,确保了云母带在导体表面的均匀覆盖。
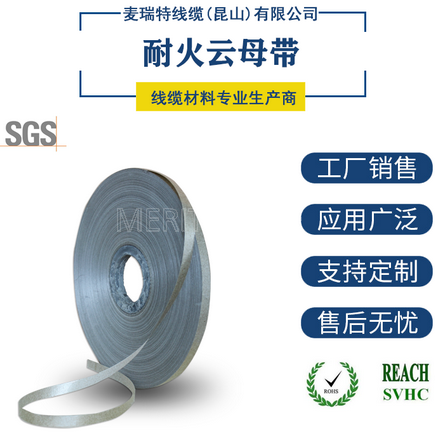
- 放卷系统:采用双工位旋转架设计,内置气动制动装置。当主工位云母带即将耗尽时,备用盘可自动切换,避免生产中断。此处的*磁粉离合器*通过电流调节输出扭矩,实现放卷速度与绕包节奏的精准匹配。
- 绕包装置:核心部件为行星轮系绕包头,其齿轮组以1:1.5的速比驱动云母带盘旋转。在导体直线行进过程中,绕包头以螺旋轨迹将云母带以55°-65°的倾角缠绕于导体表面,形成重叠率≥50%的连续保护层。
- 张力控制系统:通过*三辊浮动式传感器*实时监测云母带张力,配合PLC控制器调节伺服电机转速。实验数据显示,该系统可将张力波动控制在±0.5N范围内,有效防止云母带拉伸变形。
- 收卷系统:采用双锥度夹紧机构,配合液压驱动装置实现收卷轴自动夹持。独特的卷径计算算法,使收卷线速度始终与绕包速度同步,避免层间应力累积。
二、动态工作流程解析
云母带绕包机的工作流程可分为材料准备、绕包成型、质量反馈三个阶段,每个阶段均存在关键控制节点。
阶段1:参数预设
操作人员在HMI界面输入导体直径(Φ6-Φ40mm)、云母带宽度(15-50mm)、绕包节距(10-30mm)等参数。设备自动计算绕包角度α=arctan(节距/导体周长),并生成运动控制曲线。
阶段2:动态绕包
启动设备后,导体以0.5-5m/min的速度通过绕包头。此时*伺服电机*驱动绕包头以200-2000rpm的转速旋转,云母带在离心力作用下展开。重点在于:
- 重叠率控制:通过公式W/(πD×tanα)≥1.5(W为带宽,D为导体直径)确保耐火层完整性
- 温度补偿:内置红外测温仪实时监测导体温度,当检测到>80℃时自动提升绕包速度,防止云母带胶粘剂提前固化
阶段3:闭环调节
安装在出料口的*激光测厚仪*持续检测绕包层厚度,数据反馈至控制系统。若偏差超过±0.1mm,系统将自动调整绕包张力或修正行星轮系速比。典型案例显示,该机制可使产品合格率从92%提升至98.6%。
三、关键技术突破方向
当前行业正在推进三项技术升级:
- 多材料复合绕包:研发可同时处理云母带+玻纤布的双层绕包头,使耐火温度从800℃提升至1000℃
- 智能预警系统:基于机器学习算法,通过振动频谱分析预测齿轮箱故障,实现预防性维护
- 能效优化:将传统液压驱动改为直驱伺服系统,实测能耗降低37%,噪音值从85dB(A)降至72dB(A)
某电缆厂的应用数据显示,采用新型绕包机后,云母带损耗率由3.2%降至1.8%,单台设备年节约材料成本达12万元。这印证了设备优化对生产效益的直接影响。
四、工艺参数优化要点
要实现最佳绕包效果,需重点控制三个参数:
- 温度控制:绕包区环境温度应保持在25±3℃,湿度≤60%RH。温度过高会导致胶粘剂溢出,过低则影响贴合强度
- 绕包角度:推荐采用58°-62°倾角,此时云母带拉伸应力比45°方案降低24%,同时保证层间结合力
- 张力调节:不同带宽对应的基准张力值:
- 15mm带宽:18-22N
- 30mm带宽:35-40N
- 50mm带宽:55-60N
通过建立参数矩阵模型,工程师可快速匹配不同规格产品的工艺方案。某高压电缆项目的实践表明,优化后的参数组合使产品通过950℃/90min燃烧试验的成功率提升21个百分点。